Providing System
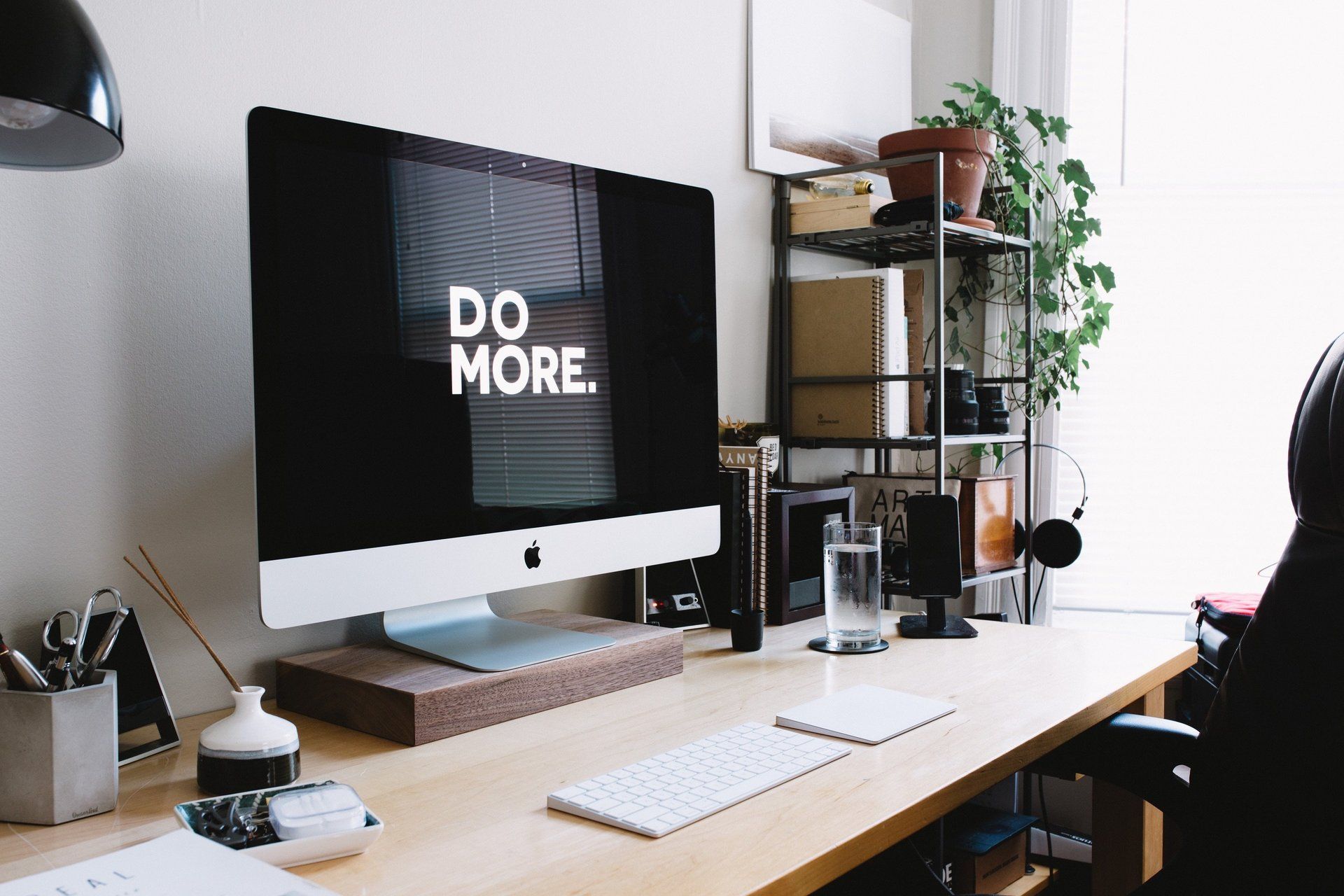
Client Background
Providing System is a 30-year-old legacy platform which is used by our client: a fully integrated steel producer. It is a complex application used to design a steel batch (Plate, Coil, Slab) based on customer requirement. The designed batch (requisition) is what starts the demand on the caster and begins the WIP process for all customer orders. The system also takes into account applying existing stock slab inventory (cold applications) to fulfil customer orders. This system is more specific to the steel industry, and the client had to put a lot of intelligence into it over the period of development.
Objective
The Sault Ste. Marie Innovation Centre (SSMIC) and its Acorn Information Solutions (AIS) division was hired to help modernize this application on a new platform and integrate it with external systems. The system needed to be easy to maintain in the future and changes be carried out with confidence if needed. The client also needed to find innovative ways to make the new system more configuration based. This was a significant project for the organization.
Project Overview
One of the biggest challenges for AIS in this project was to understand current programming logics, which was Cobol based, and then convert it to a new dimensional platform. Along with the support and knowledge from the client, the product was built in 8-9 months. The Providing System has five parts: DSPC, Plate Mill, 106 Strip Mill, Shipment Slabs, and Cold Applications. The key features of this application include:
· Ability to easily add new logics and product maintenance
· Multi-user friendly and no more distributing work via paper and pen
· Custom layout function that provides users with better visibility of current orders and can be managed more productively
· Allows granular control over functionality – modern database allows storing more data to perform analytics
This new product is easily connected with multiple third-party systems due to the modern platform. The exchange of data is very easy and turn out to be increased in efficiency for schedulers.
Benefits
The expertise provided by the client, and AIS’s ability to develop this tool makes it very unique in nature. The underline benefits include:
· Scalable solution and can fit with any manufacturing, provided with their set of logics and design
· Slick design available on smartphones or tablets
· Inbuilt security module which is useful for proper governance
· Web based application with user wise widgets and individual views
· On the fly reporting